ECCLES ENGINEERING: THE PROCESS
OUR 5 STAGE METHODOLOGY TO CREATE THE EXACT PRODUCT YOU NEED

1. INITIAL PRODUCT DESIGN, BRIEF AND QUOTATION
When a customer first approaches us they usually have a good idea of what product they would like manufactured and the annual quantity or how many pieces they would like to order.
To further aid in design, customers can provide a wide range of materials: 2D blueprints, 3D CAD models, plastic models or even real-world parts taken from a previous supplier’s run.
We will assess all costs involved from design of patterns, prototyping, sampling, testing and certification to deliver the product to customers’ satisfaction. Costs may include refining the product design or tooling for the specific product.
2. ASK THE RIGHT QUESTIONS
In order to learn as much as we can about the product to be manufactured, as experienced foundries engineers, we start the Advanced Product Quality Planning (APQP) process with a comprehensive set of questions.
We will consult with the customer to learn as much as we can about the product’s appearance, requirements and end use – it important that our engineers should fully understand the function and environment the product will be subject to during its service life.
Our foundry engineers will ask:
- What is the end use of the product or component?
- Are there regulatory or certification requirements?
- Does the current product have any tolerance issues?
- What corrosive substances will the product be exposed to?
- What level of conductivity is required?
- What specific local requirements are required for international markets?
3. USE MARKET-LEADING DESIGN AND SIMULATION SOFTWARE
We will provide the customer with a 3D model before moving forward in the product-design process. We use the latest Solid Works 3D modelling software to create, edit and improve products design.
When finished the 3D model represents an ideal version of the product in the middle of the tolerance range which will vary dependant on the final manufacturing material properties. .
Where the product is being cast in our certified manufacturing facility, we can then take that 3D model and use it as the basis for solidification simulation. The software shows how metal will behave inside a mould as it cools.
The software allows operators to experiment with various different parameters, like riser locations and pouring temperatures, to determine the best possible combination.
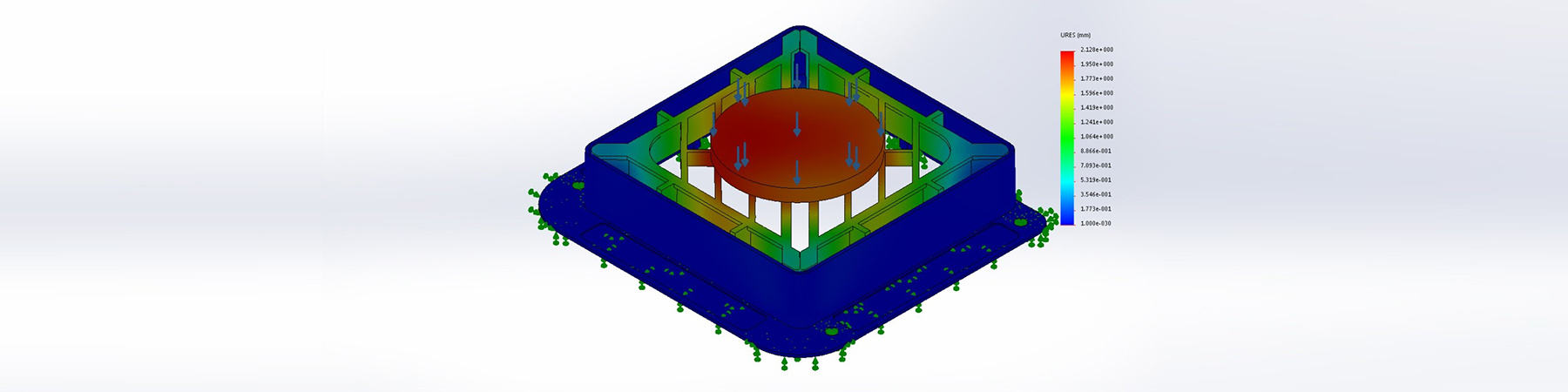
4. TEST A SAMPLE RUN
The foundry will use data from solidification software to produce patterns and core boxes and consider the gating as well as the part. We will produce moulds and carries out a sample run. At this point we will then carry out a comprehensive range of tests to ensure that the parts are within the agreed tolerance range and free of defects.
Measurements determine whether the products are within the tolerance range, by using our laser scanners, which provide a range of benefits to the customer.
Other testing, including physical inspections, x-rays and Magnetic Particle Inspection (MPI), might also be administered to ensure that there are no defects.
5. PROVIDE A COMPREHENSIVE SAMPLE REPORT
Once we have finished the sampling phase, we will send a detailed report.
We will ensure that the time and effort we have all invested results in a market product with the most efficient manufacturing plan, and we will naturally want to share this information with the customer.
The detailed report includes a PPAP checklist, including measurements, digital scans, error reports and photos. Major purchasers often require comprehensive PPAP reports like this regardless of requirements.
Along with the actual sample parts, the customer should have all the information they need to approve the product, and once approval has been given by the customer we will start production.EST A
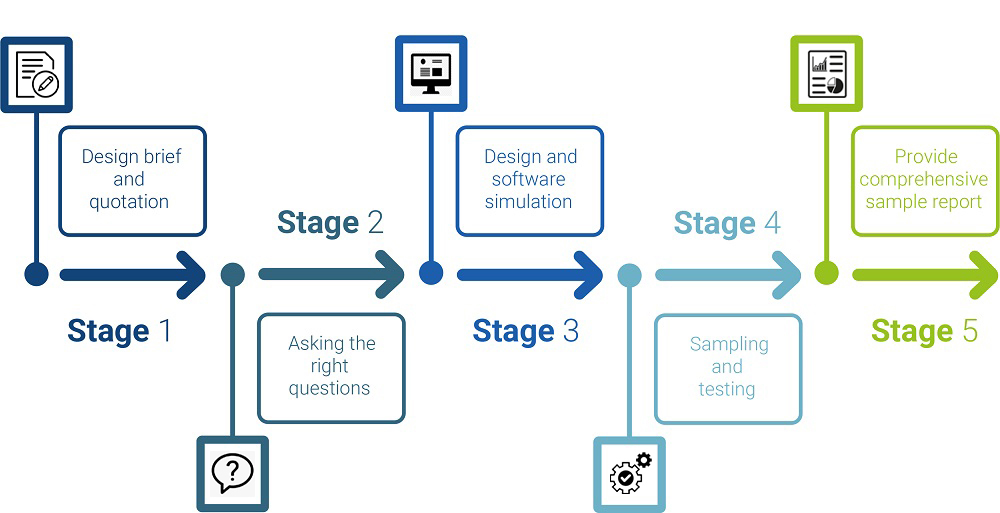