
BESPOKE DESIGN AND ENGINEERING SOLUTION
FOR ONE OF THE WORLD’S MOST FAMOUS BRIDGES
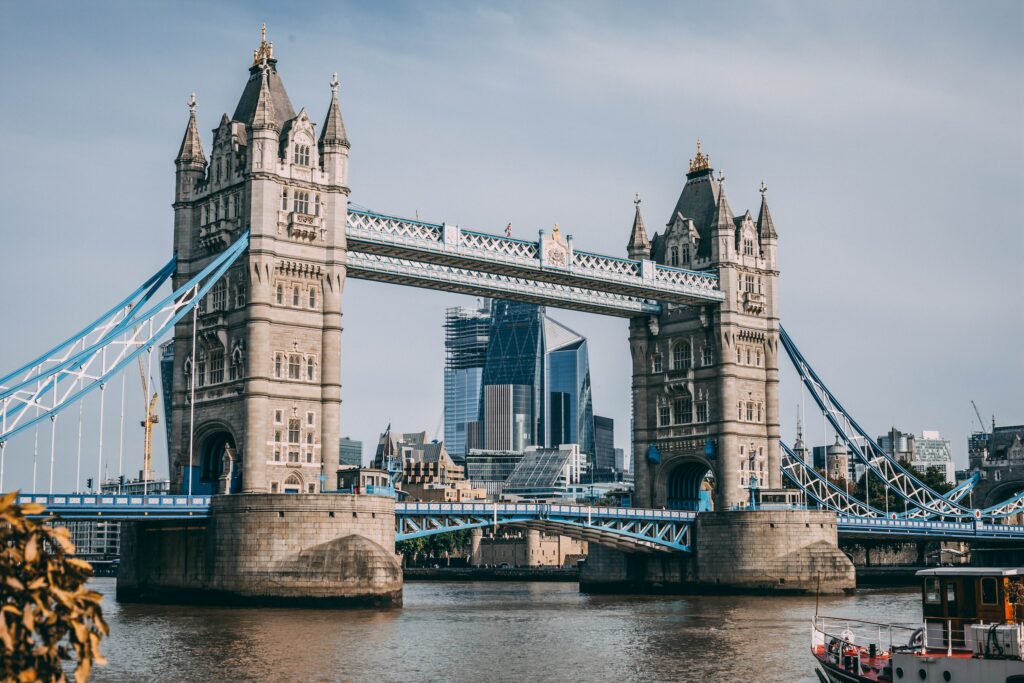
THE WORLD-FAMOUS TOWER BRIDGE
Constructed between 1886 and 1894, the iconic Tower Bridge, which crosses London’s famous River Thames, is a Grade I listed combined bascule and suspension bridge, and is one of the most instantly recognisable structures in the world.
The bridge, 240m in length, consists of two 65m bridge towers connected at the upper level by two horizontal walkways, with a central pair of bascules that are raised about a thousand times each year to allow for shipping.
The two side spans on the structure are suspension bridges, each 82m long, with suspension rods anchored both at the abutments and through rods contained within the bridge’s impressive upper walkways.
A marvel of engineering, Tower Bridge also features two giant piers, containing a staggering 70,000 tonnes of concrete, which were sunk into the riverbed as platforms to support the construction.
The bridge deck itself is freely accessible to both vehicles and pedestrians with an astonishing 40,000 people and 21,000 vehicles using it each day!
With planned upgrade activities in the works, it was an honour for the Eccles Engineering team to be approached by the City of London to consult and offer expert solutions for replacing some of the older pedestrian walkway covers.
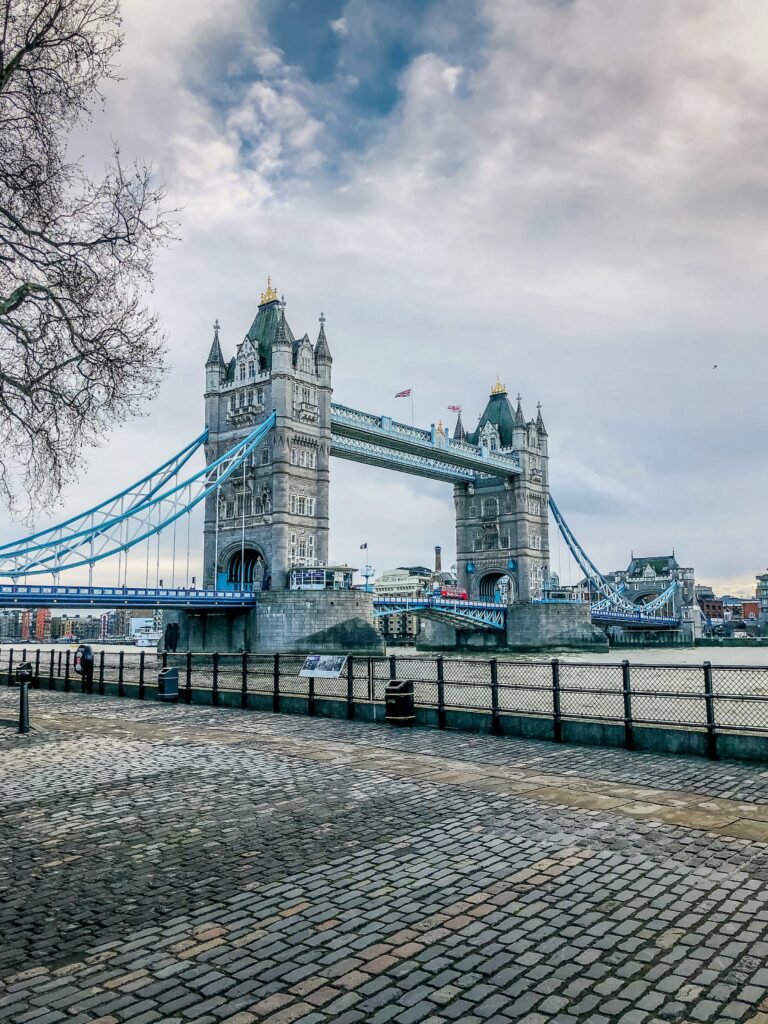
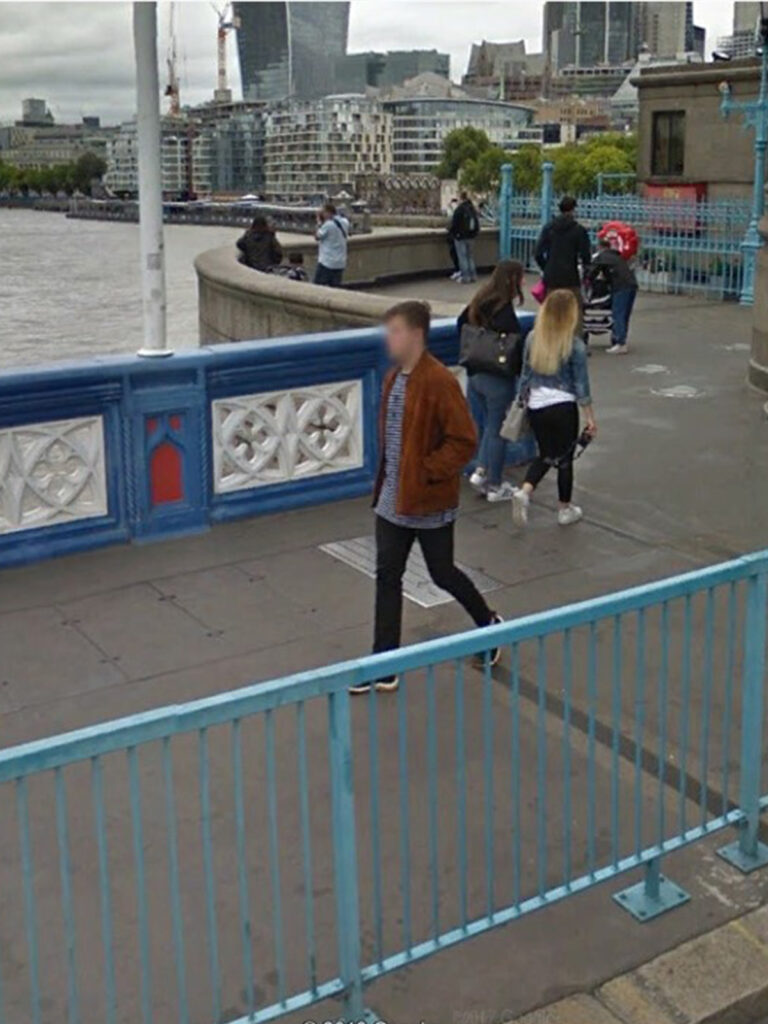
THE REMIT
Tower Bridge, a symbol of engineering excellence, presented a unique challenge to the Eccles Engineering team —replacing the worn pedestrian walkway covers with a tailor-made quality substitute whilst maintaining the bridge’s aesthetic appeal and functionality.
Many of the existing covers were old, worn and extremely heavy, posing a considerable challenge for the utilities teams needing access to the services underneath.
660 new covers needed to be bespoke-engineered that were strong yet light-weight, simple to install and manoeuvre.
These specially-designed units would replace the existing ones at four separate locations along the bridge.
THE SOLUTION
The Eccles Engineering Division quickly drew up a comprehensive design, presenting our proposals to the City of London.
Upon considering several material options, we recommended that recessed ductile iron covers would be the best solution, due to its high strength-to-weight ratio, robustness and smart aesthetics.
The covers, each measuring 1,275mm x 500mm, were bespoke designed and expertly tailor-engineered to perfectly fit the required specification, ensuring a seamless integration into the iconic Tower Bridge structure.
The units were designed with four keyholes, one in each corner, to enable easy ergonomic lifting so that the recessed covers could be removed quickly and effortlessly.
A hard-wearing, anti-slip surface was also be incorporated into the design to provide superior grip, prevent accidents and help manage the vast footfall of people utilising the bridge each day.
The design solution, with its optimised material choice, ergonomic keyholes and anti-slip safety features, reflected a considered engineering approach from the Eccles Engineering Division; one that the City of London were happy to endorse.
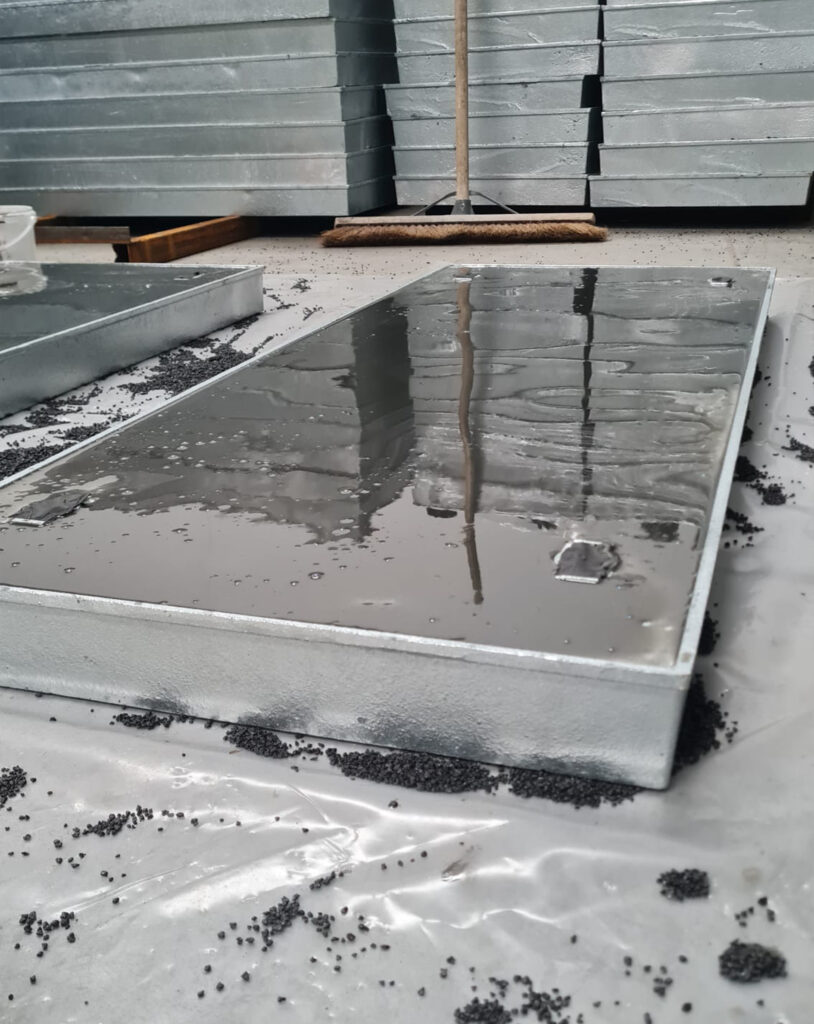
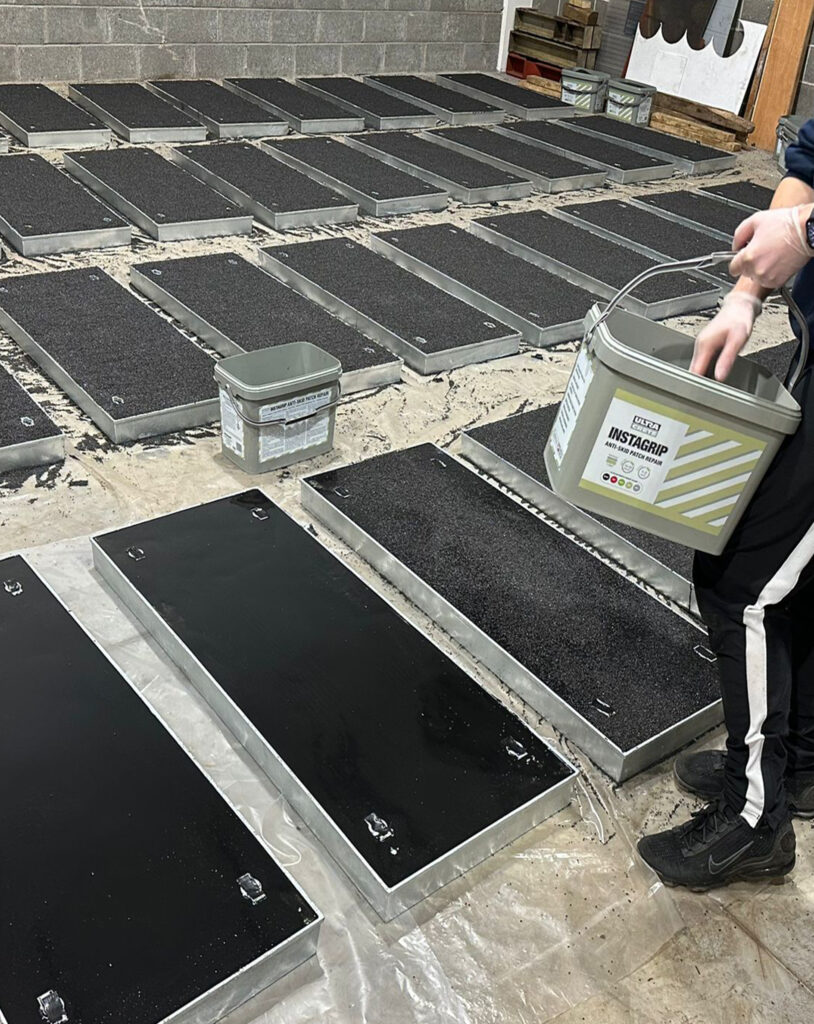
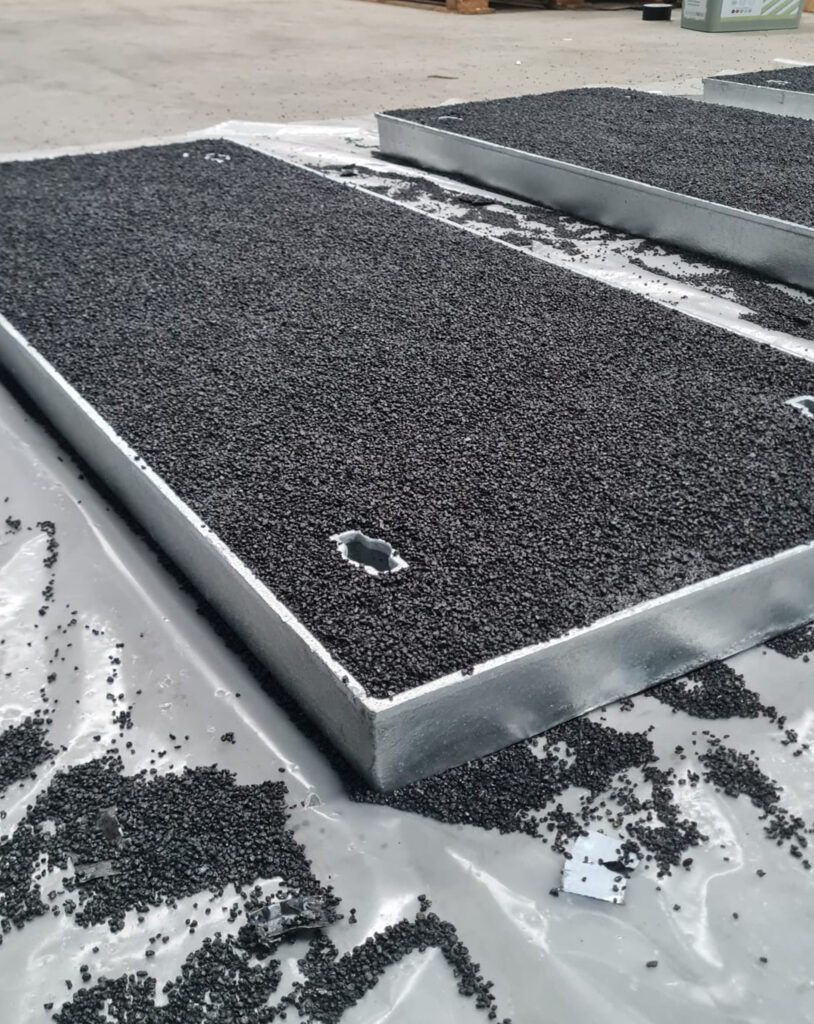
TRIAL WORKS – FEBRUARY 2021
February 2021 marked a pivotal moment with the trial installation of six meticulously engineered covers.
Eccles’ Project Director, Chris Rothery, remembers the test run:
“I wanted to be on site for the trial so we could see just how well our new cover design would fit and to help oversee the smooth transition of the product installation.
“This also gave us the opportunity to look at any other obstacles that might arise before the project went to a full scheme, when all 660 units would be replaced.
“The client advised that the trial would take place on a cold February evening when traffic to Tower Bridge would be closed off – and he was right – it was actually 2am when the trial began and it was an extremely cold night indeed!
“Our design incorporated a recessed top which would accommodate an anti-skid surfacing material and we proposed a product manufactured by Instarmac.
“We also opted for a galvanised finish to the covers. This protected the castings against the elements and also provided a neat surface finish, as we were conscious that once in situ, our covers were a highly visible element on this iconic structure.
“The trial was a huge success; the covers were a near perfect fit and the client was delighted with the outcome.”
FEEDBACK
As well as looking visibly smart on site, the newly-engineered design also successfully managed to reduce the weight of the covers from over 200kg per cover to just under 60kg for the new Eccles’ units – an astounding 70% reduction in weight without compromising structural integrity or performance.
Our post-trial report still identified one or two minor amendments that needed making to the covers, which we put forward as recommendations to the client.
These included a very slight reduction in depth and the addition of a bedding foam material under the seatings, this was to ensure an even bed onto the existing bearer bars which were to stay in place.
The trial also showed that we were able to increase the bearing area by extending the length at the bottom of the casting.
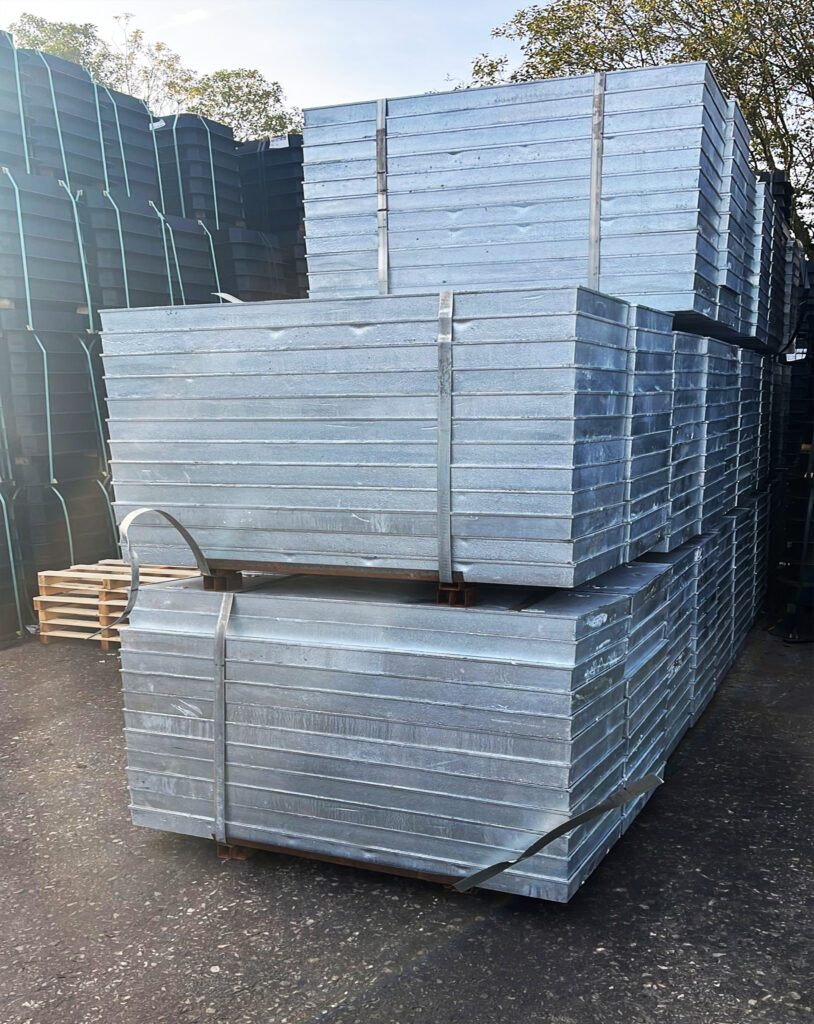
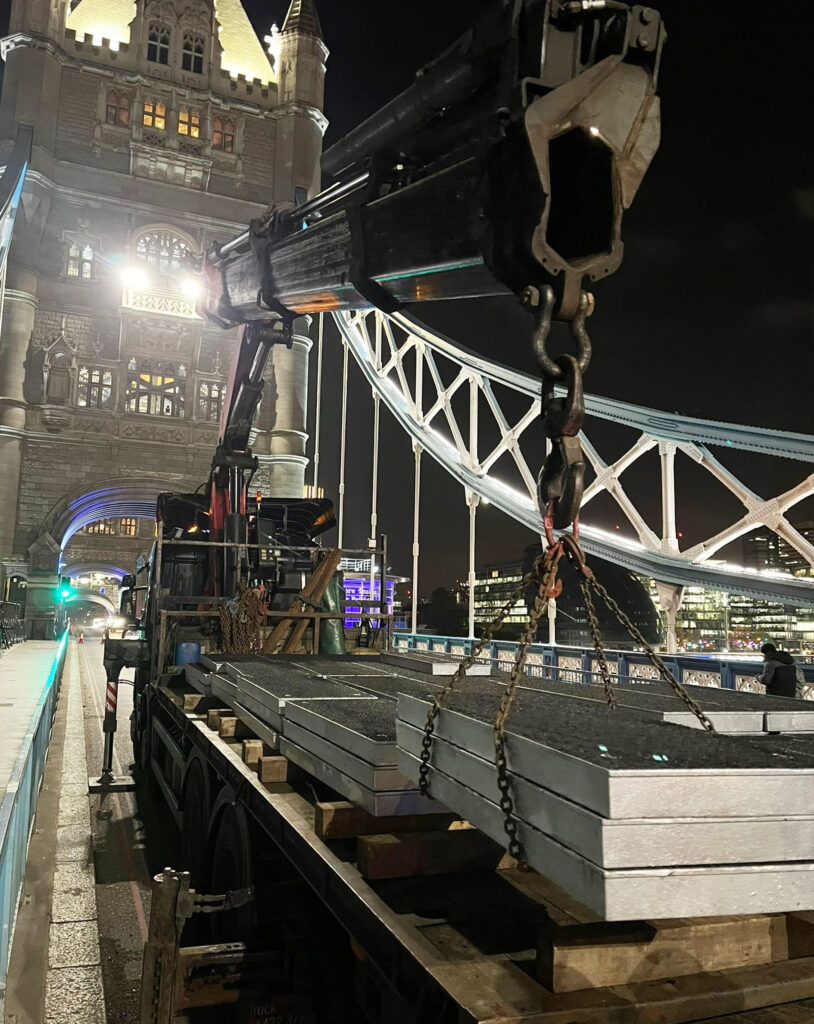
THE INSTALL – NOVEMBER 2023 AND JANUARY 2024
The new covers, 660 in total, having been manufactured to the highest standards at Eccle’s OEM facilities, were dispatched from our Walsall depot and sent first to 3RS Engineering in Rotherham, where the anti-skid surfacing was carefully added.
Once complete, the units were then transported to the Tower Bridge site. And on November 2023 the first phase of the project commenced on site, which was undertaken during the quiet of the night to minimise public disruption.
The works were undertaken in two phases; the first in November 2023 and the second in January 2024, upon completion of the scheme.
Eccles’ Project Director, Chris Rothery, was once again keen to oversee the project at this critical first stage.
“Liasing with both the client and 3RS, we ensured they had enough covers on a weekly basis, so the anti-skid material could be applied and nightly deliveries to Tower Bridge could be pre-planned well in advance as to maximise the working hours on site.
“The application of the Instarmac material was a critical part of the project and 3RS had to carefully plan these production runs. As covers were completed and despatched to site by 3RS, Eccles delivered the next batch, so far this has run like clockwork between our two companies.
“We’re thoroughly delighted with how the scheme has progressed to date; feedback from site managers has been great and installation is going really well.
“Eccles Engineering look forward to completing this project in January.”
Adam Eccles, Managing Director said:
“Securing the opportunity to collaborate with the City of London and our contractors represents a defining moment for Eccles UK and one of the proudest moments of my career.
“As Managing Director, I am overflowing with pride for our Engineering Division, whose skill and commitment were crucial in securing this prestigious project.
“This achievement goes beyond mere business growth; it’s about integrating our legacy alongside a world-renowned landmark, acknowledging the progress our company has made in recent years, and showcasing our skill and ability to design, create and conceptualise key engineering solutions to fulfil high profile global projects.”
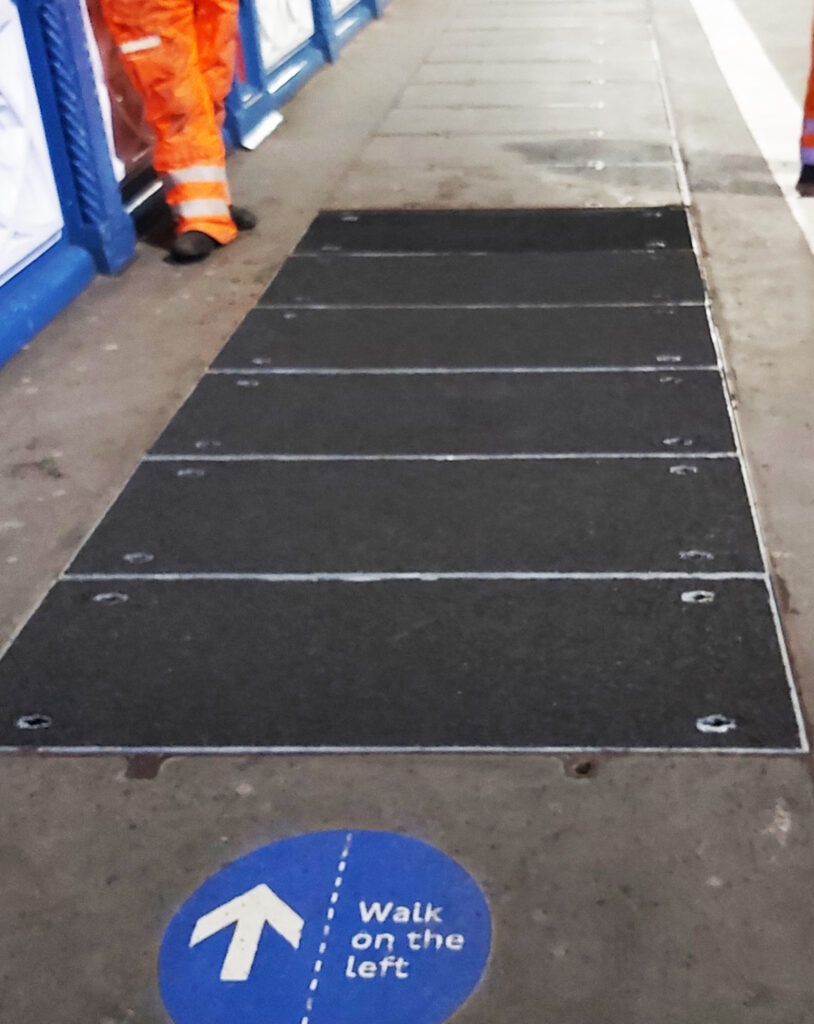
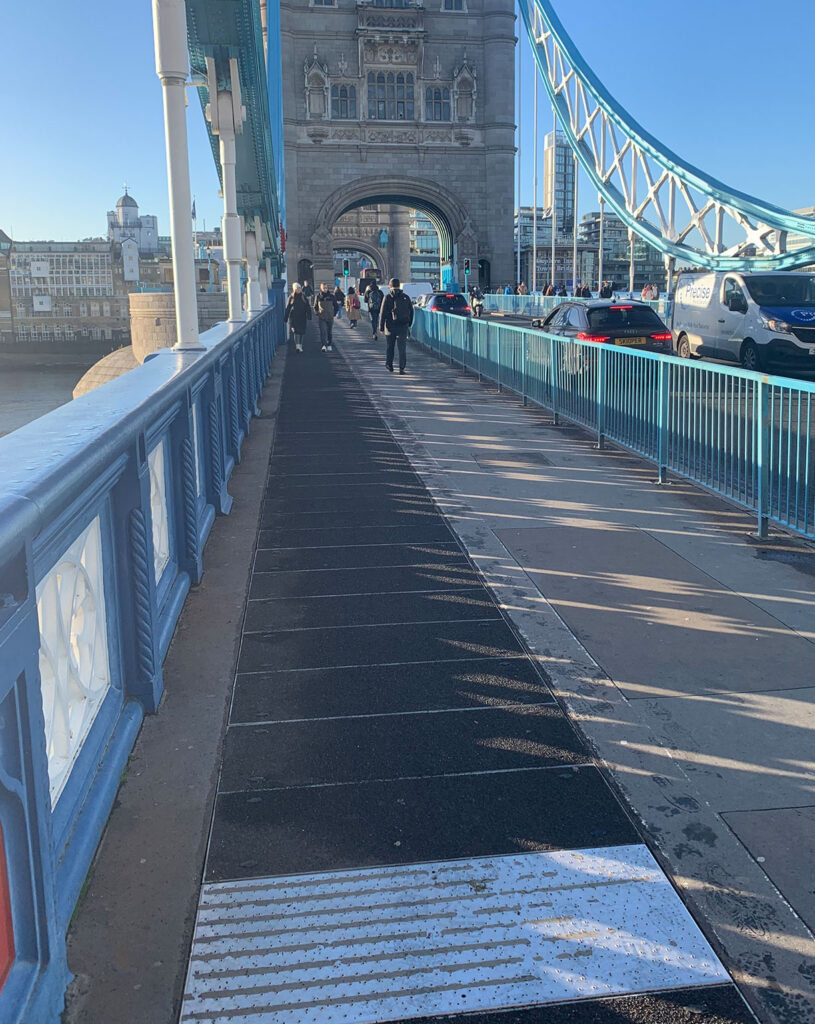
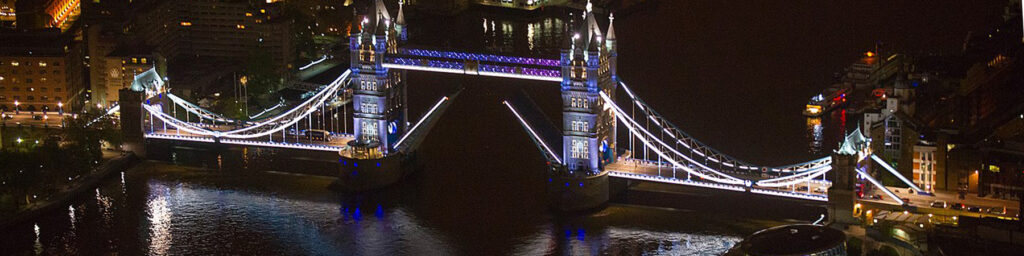
OUR THANKS TO THE CITY OF LONDON
We would like to thank the City of London Engineering Department for trusting us with this very special project and to our contracting client FM Conway for their support and regular updates as the project progressed.
Eccles will be doing a follow-up project profile in January 2024 as we commence the second phase of the scheme to completion.
For more information and facts about Tower Bridge please visit: www.towerbridge.org.uk
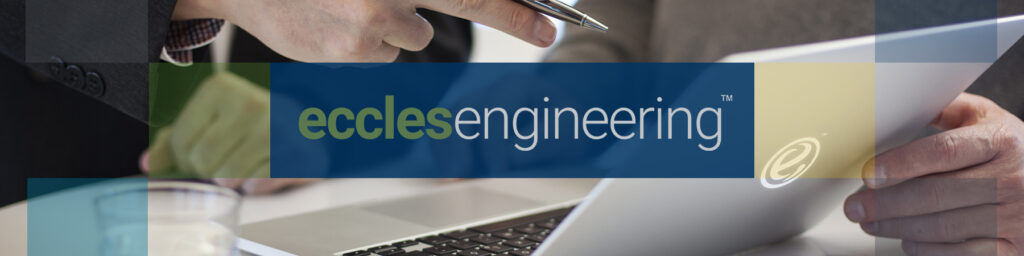
BESPOKE DESIGN AND ENGINEERING SOLUTIONS
If your project has a bespoke requirement, Eccles Engineering is ready to help. Our specialist design and development team will work with you to realise the exact specification of your project, designing and engineering a quality and cost-effective solution that’s tailored just for you.
CLICK HERE to visit the Eccles Engineering Division.